When you’re bringing a product to market, anything that shortens the production cycle or raises confidence in the end-product is a competitive edge. Urethane casting is a process with a number of special features that really shine during the early manufacturing process.
Let’s dig into cast urethane molding, its benefits, and how it works.
What is Urethane Casting?
Stated by urethane manufacturers, urethane casting is a time-tested molding process. It can be used to make parts almost as quickly and flexibly as 3D printing, but with the strength and appearance of injection molded parts.
Cast urethane molding is a great option for early prototyping and show models as it’s significantly cheaper than injection molding. The process involves creating a model of the part to be produced and using it to make a silicone mold which is then filled with urethane.
It looks like this:
Master Plan
- Once your CAD file is finished, a master pattern is then created.
- The part is 3D printed with SLA or PolyJet technology or CNC machined.
- The master pattern is then prepared for molding with any required surface finish or inserts.
Creating a Mold
- The master pattern is suspended in a box and silicone is poured around it.
- Once the silicone has cured, the mold is carefully cut into two pieces which can be fit back together precisely.
- The master pattern can now be removed and the mold is ready for use.
Urethane Parts are Cast in the Mold
- Once the best urethane mix for your part is determined, the mold can be filled and allowed to cure.
- The urethane parts are carefully removed from the mold so that it can be reused or refurbished for reuse.
Parts are Finished and Shipped
- The parts are now cleaned and if they need paint or other surface coatings, it is applied before being packed and shipped to you.
Why is Urethane Casting Better?
Speed
Regardless of your industry, cutting time from the production cycle is a money saver.
Urethane casting has a fast turnaround time, typically 2-4 weeks, with the first parts available even earlier when necessary. Printing the master pattern and producing the silicon mold can usually be finished within a few days.
Compare this with injection molding, which often takes a minimum of 6 weeks to return the first parts. Whether you need to beat competitors to market or get a concept ready for display, this speed is a big bonus.
A faster turnaround also means that designers and engineers can get a prototype in their hands faster, and with the strength and durability of urethanes, this prototype can be a realistic representation of the end product.
This means that realistic tests can be accomplished sooner. Even if time isn’t a concern, a faster turnaround between redesigns means that more rounds of testing can be completed if necessary.
Affordable Prototype Parts
When you’re working on a new design, quality parts are essential to getting a realistic idea of how the final product will work and respond to different situations. If prototype parts are too different from the final product, test results can be skewed or even useless.
Cast urethane molding is significantly cheaper than injection molding or other options, while still providing high-quality parts with properties similar to those of the end product.
Urethane prototype parts can expedite the testing process while keeping multiple rounds of testing within your price range.
Options for Consistency and Finish
Urethanes can be mixed to feature a wide variety of properties:
- The color of cast urethane parts can be matched to exact shades or even be transparent.
- The molding process allows for high-quality surface texturing.
- You choose the hardness of your part, from very hard, to flexible or even rubbery. (Shore durometer ratings range from 10 shore A to 85 shore D.)
- Cast urethane molded parts are also ideal for multi-durometer parts that need varying levels of hardness throughout.
- A wide variety of additives are available for special use-case parts that need specific properties, including ESD protection, fire retardancy, adhesives, chemical resistance, heat resistance, and more.
- In addition to altering the material, embedded hardware like inserts can easily be added to the part during the molding process.
Thanks to these possibilities, cast urethane molding can produce prototypes that are very similar to injection molded end products and it’s even possible to produce low-volume runs of finished parts.
Multi-durometer parts are also a unique feature that can’t be had from some other production processes.
Durability 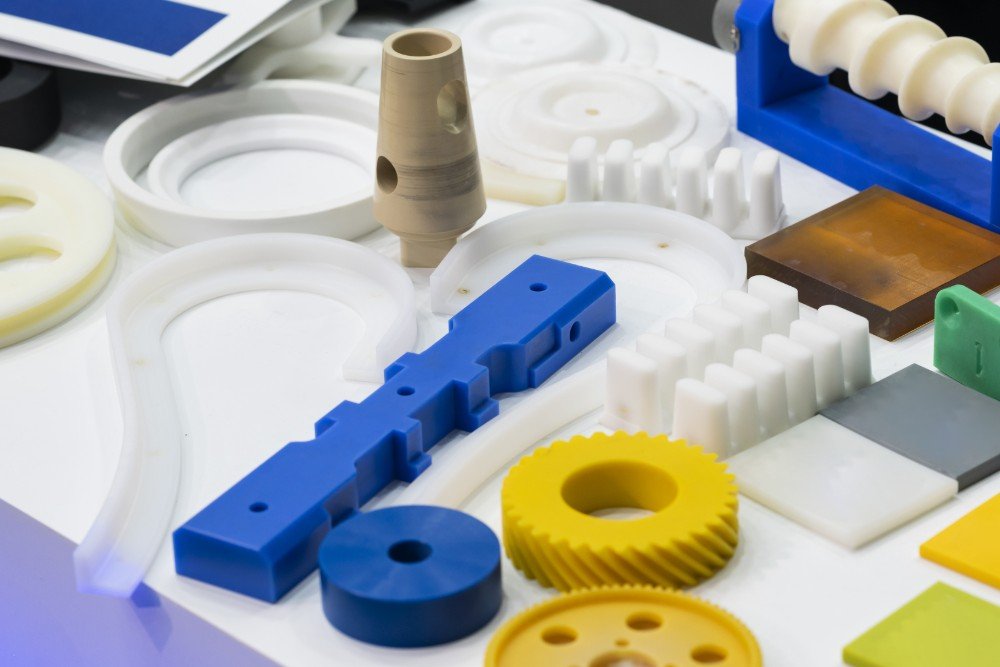
Durability is a top priority when developing your product. When handling your product or model, investors and potential customers want to feel reassured that it will survive regular use.
In a world of low-cost disposable products, the sturdiness of your product can be a real selling point. Urethane is highly resistant to wear and tear. It’s resistant to abrasion and vibration, tear-resistant, UV-stable, and can be tolerant of extreme heat or cold.
If you choose urethane parts for your product or prototype, you can rest easy that it will withstand sustained use and testing.
Accuracy
When you’re ready to test your product, you want to know that the parts that you’re using really represent the parts that will be used in the final product. While there are a lot of options when it comes to prototyping, the accuracy of cast urethane parts is second to none.
Urethane has a very low shrinkage rate when curing, typically +0.15%, which means that casted parts will very closely match the master pattern that they were made from. Accurate parts translate to an accurate understanding of the performance of your final product, improving confidence for engineers and shareholders alike.
Does cast urethane molding sound like a good fit for your company’s next manufacturing process? If you need a small run of high-quality parts, the price and quality of urethane casting can’t be beaten.
If you need accurate prototype parts quickly, cast urethane molding is for you. If you need a one-off model for a show that has the quality of an end product, urethane casting is your best bet.