You might have a general idea of how the polyurethane manufacturing process works, but knowing the details will help you out early in your career. A better understanding of this subject could also help you figure out which expenditures and timelines create issues in your current processes. Do you know how to reduce costs and pull in timelines in one sweep? We do—and we share our tips with you below.
What is Polyurethane?
Polyurethane is a synthetic type of resin that has polymer units linked by groups of urethanes. These are mainly used in varnishes, paints, adhesives, and foams that are important in almost every industry, from medical to automotive.
If you’re a polyurethane manufacturer, you’re a critical part of many people’s lives each and every day—even if it is behind-the-scenes. It’s crucial your polyurethane manufacturing process is up-to-par so you can keep serving the public and making money for you, your family, your stakeholders, and your dedicated employees.
The Process
Figuring Out Custom Options
Before starting on the real polyurethane manufacturing process, you need to know what type of product you’re making and what specs it needs. There are countless combinations and design variables you can choose from to make exactly what you’re looking for.
For instance, you might want something with a certain elasticity, hardness, tear strength, chemical resistance, flame resistance, abrasion resistance, strength—or a slew of other characteristics. Precise specifications are possible with the right mixture.
Mixing Ingredients
Diisocyanates are a group of versatile building blocks, so to speak. They’re used to make a range of polyurethane products. Mixing them with other chemicals create some of the most valuable and essential polyurethanes. It’s like baking—simply mix all the ingredients together, and you get your desired end product.
It’s rather incredible that polyurethane can be made into so many different types of items—something as soft as a pillow or as hard as a car bumper. Of course, it might take some trial and error with multiple rounds to find the perfect mixture required, but in the end, it will be worth it.
Insertion Into Mold 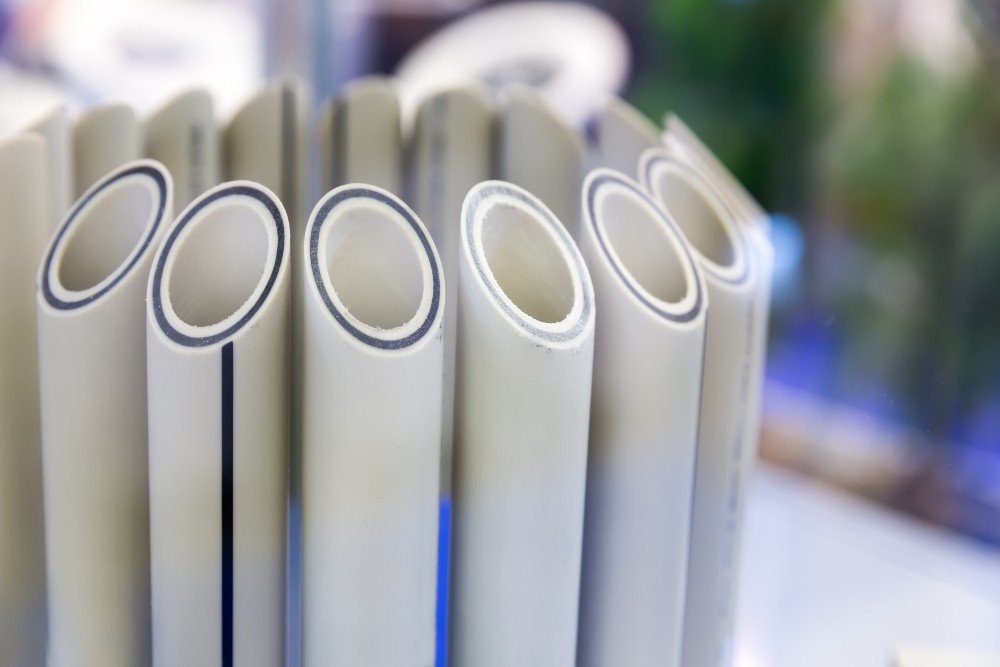
This is where the magic happens. There are different ways you can create your product in the polyurethane manufacturing process. You can use compression molding, open cast molding, spin casting, or injection molding.
For compression molding, the polyurethane will be in liquid form. You’ll pour it into a mold, which is placed into a compression press. The heat thickens the liquid and the pressure completes the molding process.
Open cast molding also starts in a liquid form, but it goes into an open mold which needs heat from a special oven to finish it off.
Spin casting involves a spinning mold. You’ll pour the liquid polyurethane in while this is happening to remove any air trapped inside.
Finally, with low-pressure injection molding, you’ll inject the liquid form of the substance into a mostly closed mold. The mold has openings that allow air to slowly escape.
Final Touches and Product Inspection
After the product cools down and comes through the molding process, it’s shaved down to the required size. It’s shaved down farther when excess pieces of polyurethane parts get caught outside the mold and need to be touched up for consistency. Once the product is almost ready to go, it moves through an inspection for quality control.
Packaging
Last, but not least: when the product has been approved, it goes onto the packaging phase. The facility you use for your polyurethane manufacturing process may or may not do this for you, so this step can depend on your situation.
Regardless, you want to make sure every package with your brand attached is of the best quality. Your products should be well-protected and look professional so stakeholders keep coming back for more.
The Future of Polyurethane
Polyurethane is gaining traction over alternatives because of its environmental advantage—plastic is not environmentally friendly. Engineers are always experimenting with new mixtures and chemicals to arrive at unique compositions—making polyurethane more versatile and beneficial than ever.
One trend gaining popularity lately is replacing toluene diisocyanates with less-volatile polymeric isocyanates—but there are always developments in the field. Knowing how the polyurethane manufacturing process works will help you think up, plan out, and create better products while cutting costs, saving time, and more. Whether your focus is inventory build-out or improving your manufacturing procedures, you can use this guide as a fundamental explanation of how polyurethanes are made.